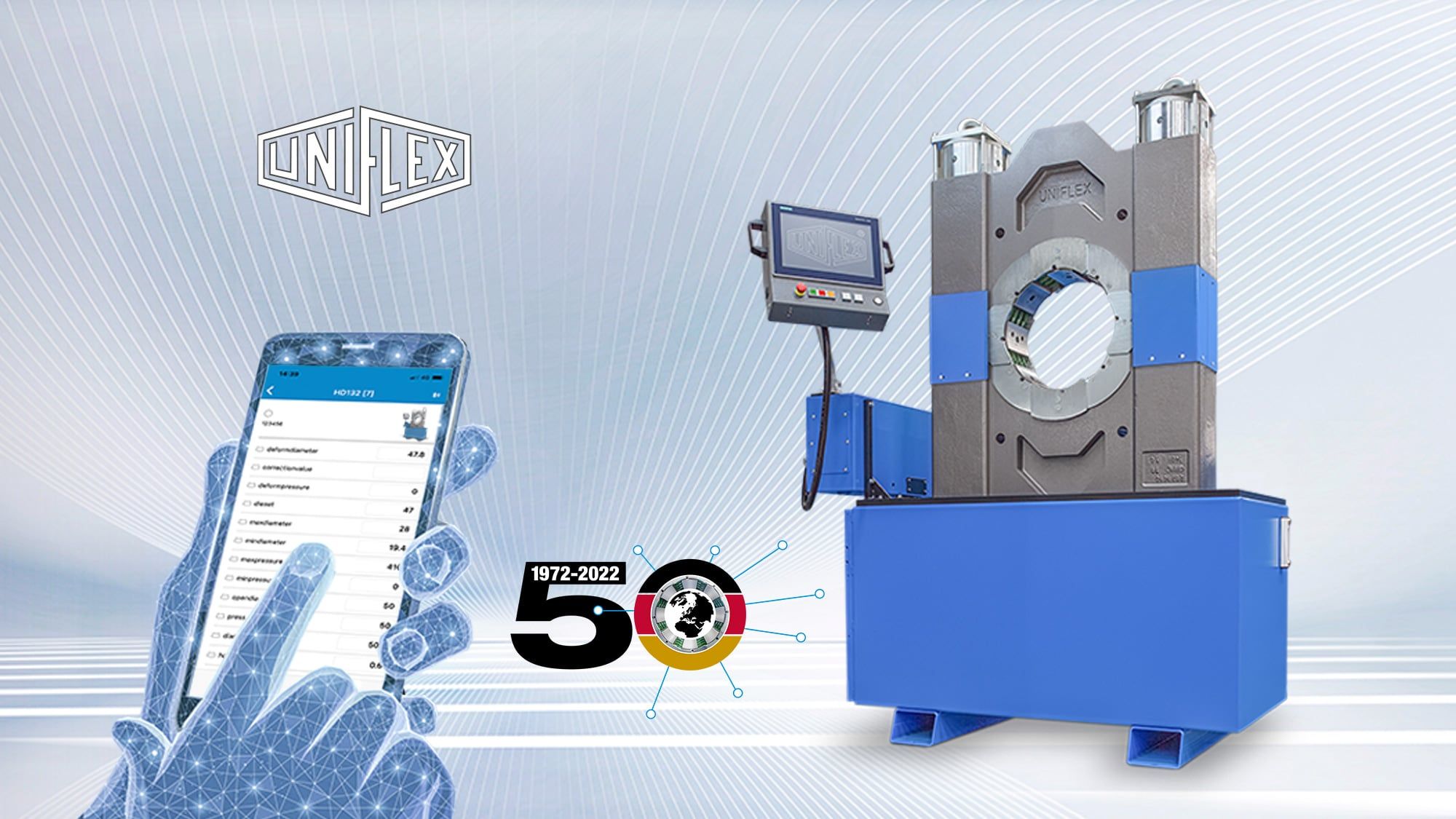
INDUSTRIE 4.0
UNIFLEX: 50 Jahre auf dem Weg in die Zukunft
Die UNIFLEX Hydraulik GmbH mit Sitz in Karben bei Frankfurt entwickelt, produziert und vertreibt seit 50 Jahren innovative Systeme für die Herstellung und Bearbeitung von Schlauchleitungen. Das Unternehmen mit seinen Niederlassungen und Tochtergesellschaften in Amerika und Asien beliefert den gesamten Weltmarkt. Über 85% der UNIFLEX Produkte werden exportiert, u. a. an Marktführer wie Caterpillar, Gates und Parker.
UNIFLEX gewährt auf alle Maschinen eine Garantie von zwei Jahren.
UNIFLEX Hydraulikpressen zeichnen sich aus durch die einzigartige Gleitlagertechnik: Im Gegensatz zu geschmierten Pressen arbeiten UNIFLEX Pressen nahezu ohne Reibungsverluste. Das reduziert die Wartung auf ein Minimum, denn „Pressen ohne Schmieren“ ist sauberer und weniger arbeitsintensiv. Zudem sind Maschinen von UNIFLEX bekannt für bestmögliche Arbeitsergebnisse, zuverlässigen Return-on-Investment und maximale Ergonomie. Ein umfassendes Programm an Zubehörteilen macht das Arbeiten mit verschiedenen Geräten noch einfacher.
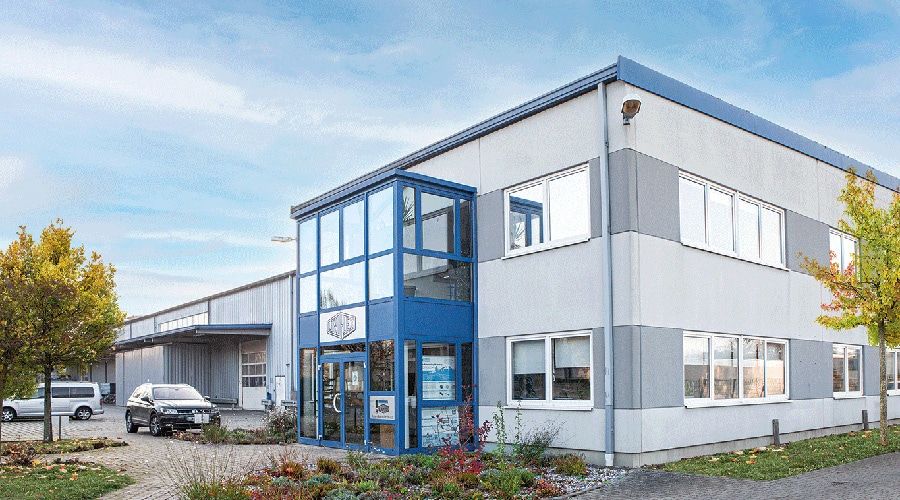
The best Return on Investment
Wirtschaftlichkeit, Nachhaltigkeit und Klimaschutz mal anders gedacht:
Logisch: Wer ökonomisch arbeiten und sparen möchte, schaut auf das Geld. Doch wer schlauer sparen möchte, der schaut nicht nur auf den Anschaffungspreis, sondern auch auf die Betriebskosten und die Lebensdauer von Investitionsgütern.
Mit der Erfindung der Gleitlagertechnologie hat die Erfolgsgeschichte von UNIFLEX vor 50 Jahren begonnen – und jetzt wird ein weiteres Kapitel aufgeschlagen. Die nächsten 50 Jahre UNIFLEX. Die Gleitlagertechnologie macht die Maschinen zwar etwas teurer als (eigentlich nicht) vergleichbare Pressen mit aufwändiger Ölschmierung, dafür aber wesentlich nachhaltiger, weil langlebiger und kostengünstiger in Sachen Energieverbrauch und Wartungsaufwand – und mit einer besseren CO2-Bilanz.
Die Gleitlagertechnologie reduziert den Presskraftverlust um bis zu 20% durch weniger Reibung zwischen den sich bewegenden Teilen der Maschine. Dies führt zu einem bis zu 20% geringeren Energieverbrauch. Weitere Vorteile sind die höhere Sauberkeit bei der Arbeit für Mensch, Werkstück und Maschine.
Nachhaltigkeit zahlt sich aus
Hydraulikpressen mit Gleitlagertechnologie von UNIFLEX bietet einen unschlagbaren Return on Investment – im Vergleich zu geschmierten Pressen und auch bei anderen Investitionen.
Der Wechsel von Gleitlagern, Öl, Federn und eine Revision alle 2 Jahre kostet bei einem Lebenszyklus von durchschnittlich 23 Jahren etwa 14.000 €. Addiert zu einem Maschinenpreis von 20.000 € ergeben sich 34.000 € Gesamtkosten für 16.000.000 Pressvorgänge.
Außerdem nimmt die Gleitlagertechnologie gerade mal 2 Minuten an Service pro Woche in Anspruch, um die Ablagerungen abzusaugen. Geschmierte Maschinen benötigen neben dem Säubern rund 7 Minuten um das Schmiermittel einzubringen.
Damit reduzieren sich die Kosten je Pressvorgang auf sagenhafte € 0,0021!
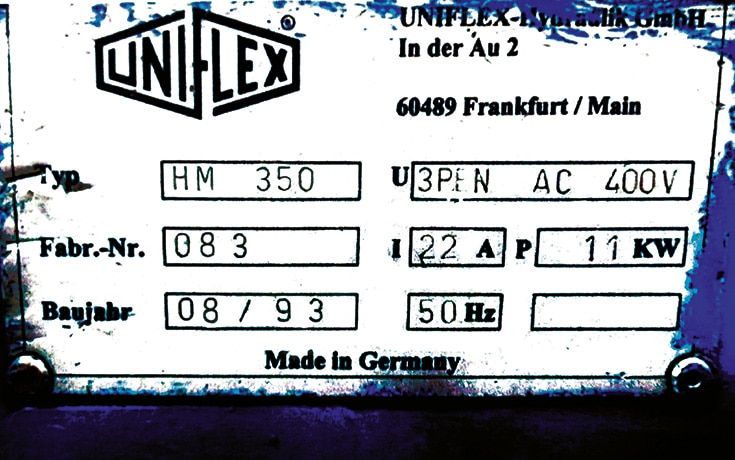
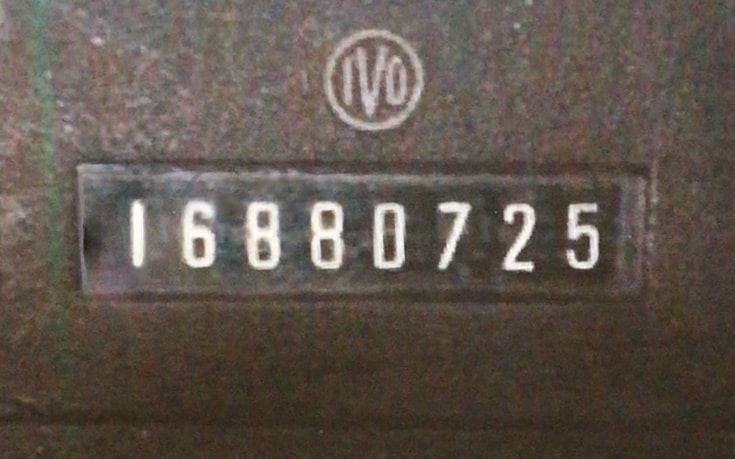
Wie spart man mit UNIFLEX > 70% CO2 ?
Indem man Gewicht reduziert und die Lebensdauer verlängert.
Gutes Engineering mit einem Energie-Verbrauch von 4 kW (Wettbewerb: > 5,5 kW) und eine starke, langlebige Konstruktion sind das BESTE für unsere Zukunft!
Eine Maschinen-Lebensdauer von 30 Jahren
anstatt 2 Maschinen je 15 Jahre.
* 1 Tonne Roh-Stahl entspricht 1,7 Tonnen CO2
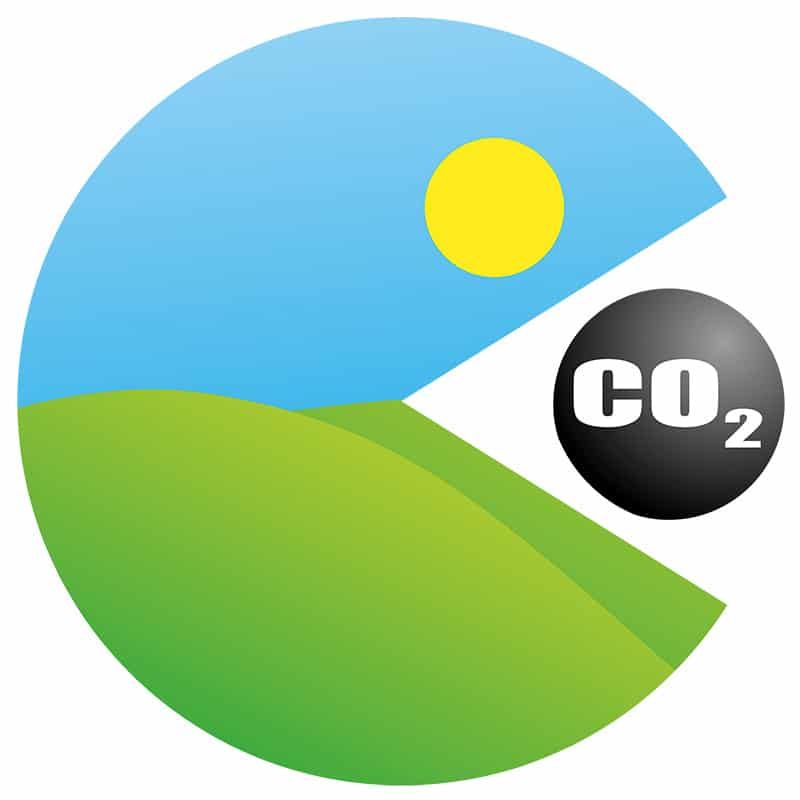
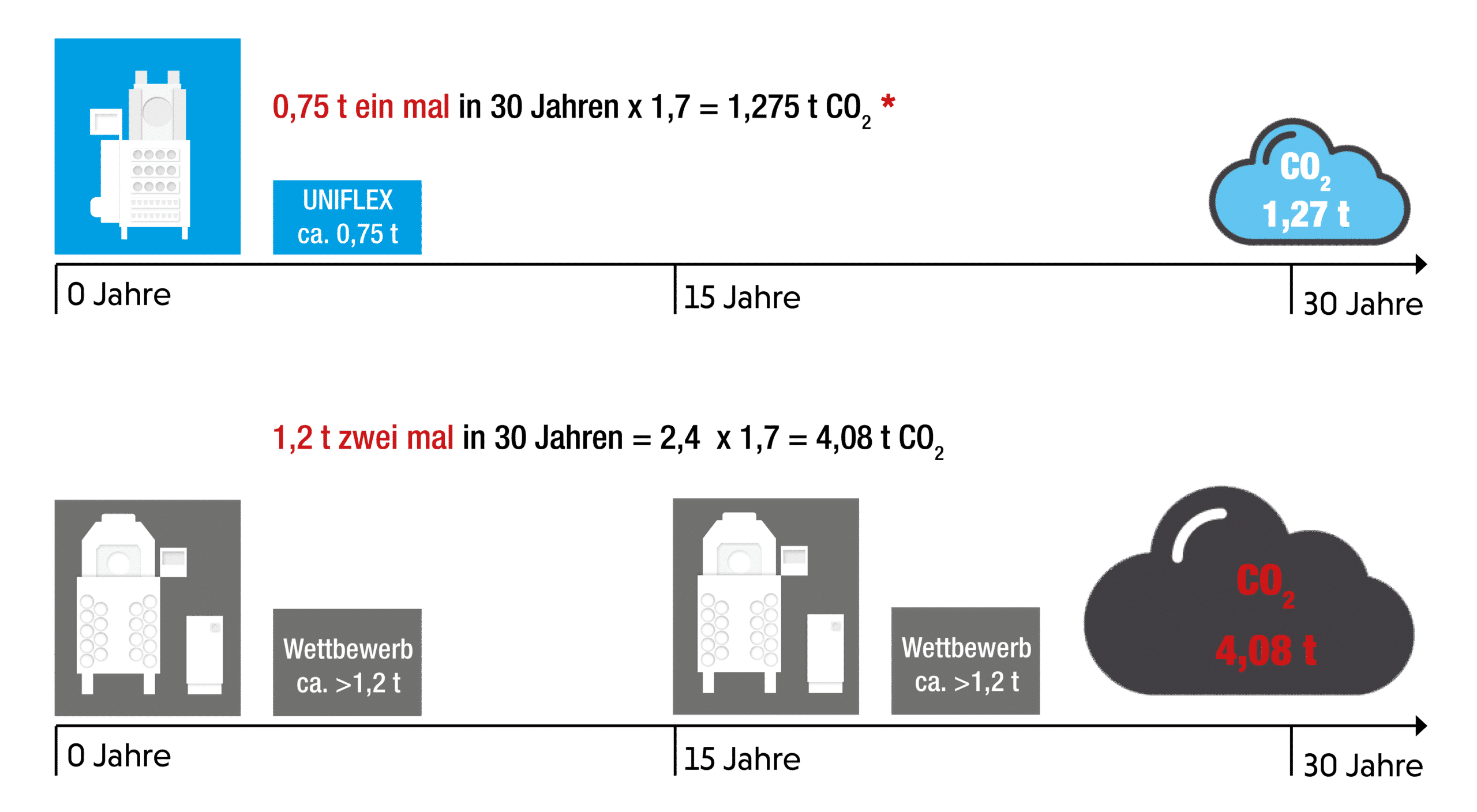
Digitalisierung
Die Vernetzung von Mensch und Maschine
Alle Welt redet von der digitalen Transformation, UNIFLEX handelt – schon lange. Um seinen anspruchsvollen Kunden innovative, computergesteuerte Geräte bieten zu können, hat UNIFLEX nach der mittlerweile schon jahrelang bewährten Steuerung Control C.2 das UNIFLEX Wireless Management System (UWMS) entwickelt.
Mit dieser komplexen Software lassen sich Artikeldaten auf einem Server speichern und sämtliche Ergänzungen immer updaten. Via Internet können Anwender dann eine App auf ihr Smartphone oder Tablet laden und anschließend den Press-Auftrag per Bluetooth direkt an die Schlauchpresse senden.
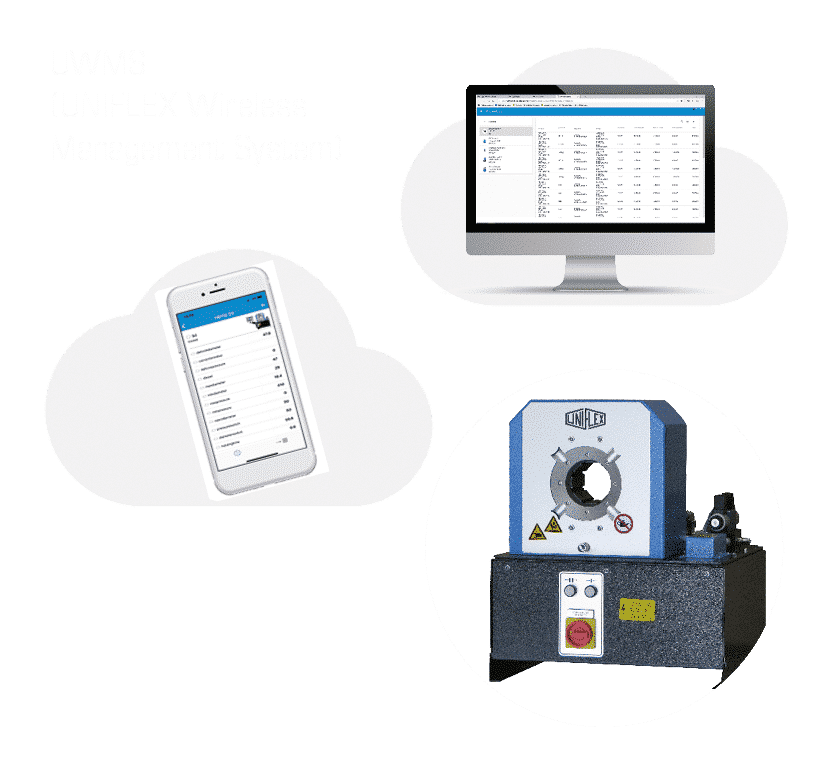
Vorteile
- Aktuelle Pressdaten halten Kunden und Anwender jederzeit auf dem neuesten Stand.
- Alle Daten installierter Hydraulikpressen lassen sich jederzeit abrufen (Anzahl der Pressungen, Details darüber, was verpresst wurde plus der Daten, die während des Press-Vorgangs aufgezeichnet wurden).
- Das Einpflegen von Seriennummern ermöglicht es, stabile Systeme für Tracing und Nachbestellungen zu erstellen.
- Auch Datenanalysen und Reportings wie z. B. Marktbewertungen lassen sich einfach erstellen.
Die Maschinen-Manufaktur
Bei UNIFLEX gibt es keine Fließbänder und keine Großserienfertigung. Die Schlauchpressen und alle anderen Geräte und Maschinen werden im klassischen Manufakturverfahren hergestellt, von Hand und größtenteils nur auf Bestellung. Jede Presse ist daher ein sorgfältig, von gut ausgebildeten Fachkräften, montiertes Einzelstück „Made in Germany“.
Auch Sonderanfertigungen und kundenindividuelle Varianten sind daher jederzeit machbar.
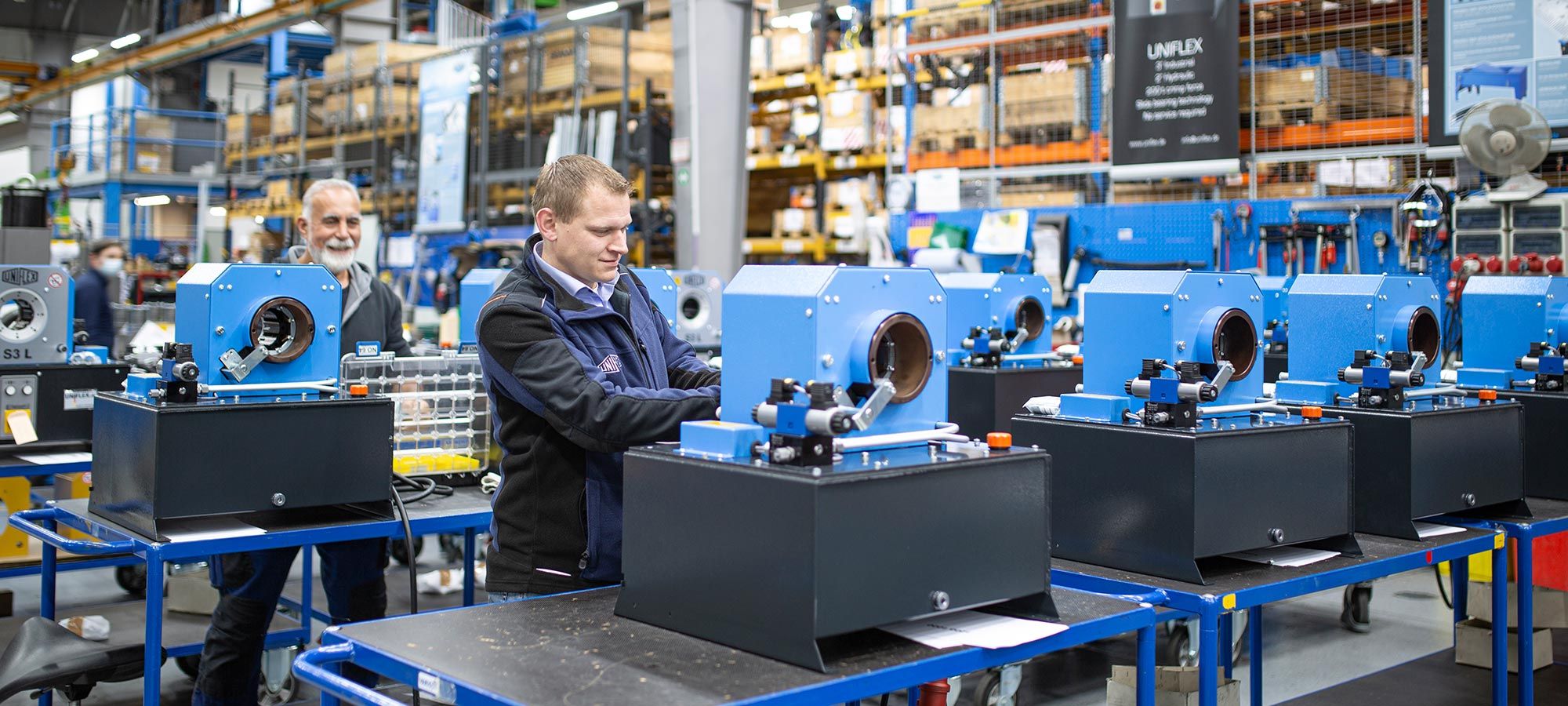
Innovation und modernste Qualität
Aufbauend auf dem Innovationsvorsprung durch die Entwicklung der Gleitlagertechnologie vor 50 Jahren arbeitet UNIFLEX bis heute stetig an der praxisnahen Weiter- und Neuentwicklung nachhaltiger und ergonomischer Maschinen für die Schlauchherstellung und -reparatur.
Zwei Jahre Herstellergarantie
Von Anfang an und auch in Zukunft bietet UNIFLEX volle zwei Jahre Funktions- und Materialgarantie auf alle Geräte.
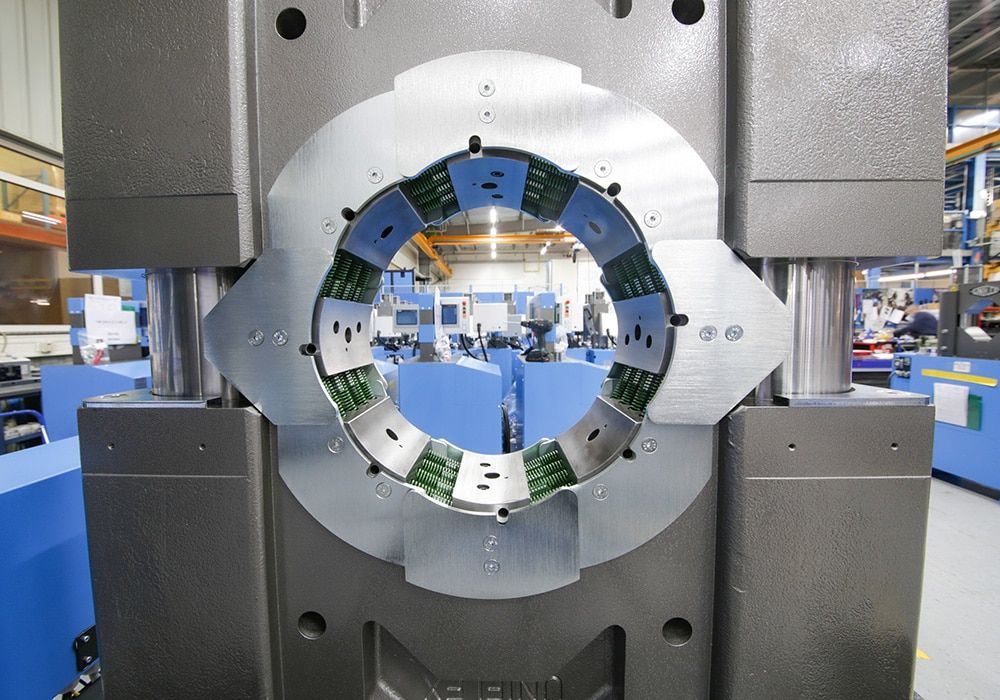
1972-2022: 50 Jahre Innovation & Nachhaltigkeit in der Schlauchverarbeitung
1972 wurde die UNIFLEX-Hydraulik GmbH in Frankfurt am Main gegründet. Dank bahnbrechender Innovationen und außerordentlicher Produktqualität entwickelte sich das florierende Unternehmen schnell zu einem der weltweit führenden Anbieter von Maschinen zur Herstellung von Schlauchleitungen.
Heute, nach 50 Jahren, ist UNIFLEX der Systemanbieter in Sachen Schlauchleitungsherstellung – von der Werkstattausrüstung bis zur Produktionsanlage. Ebenso innovative wie zuverlässige und langlebige Schlauchpressen, Trennmaschinen, Perforiergeräte, Schälmaschinen, Prägegeräte, Prüfsysteme, Software und Reinigungsgeräte wurden und werden in enger Zusammenarbeit mit führenden Schlauchleitungskonfektionären und Anwendern in aller Welt entwickelt und weltweit vertrieben.